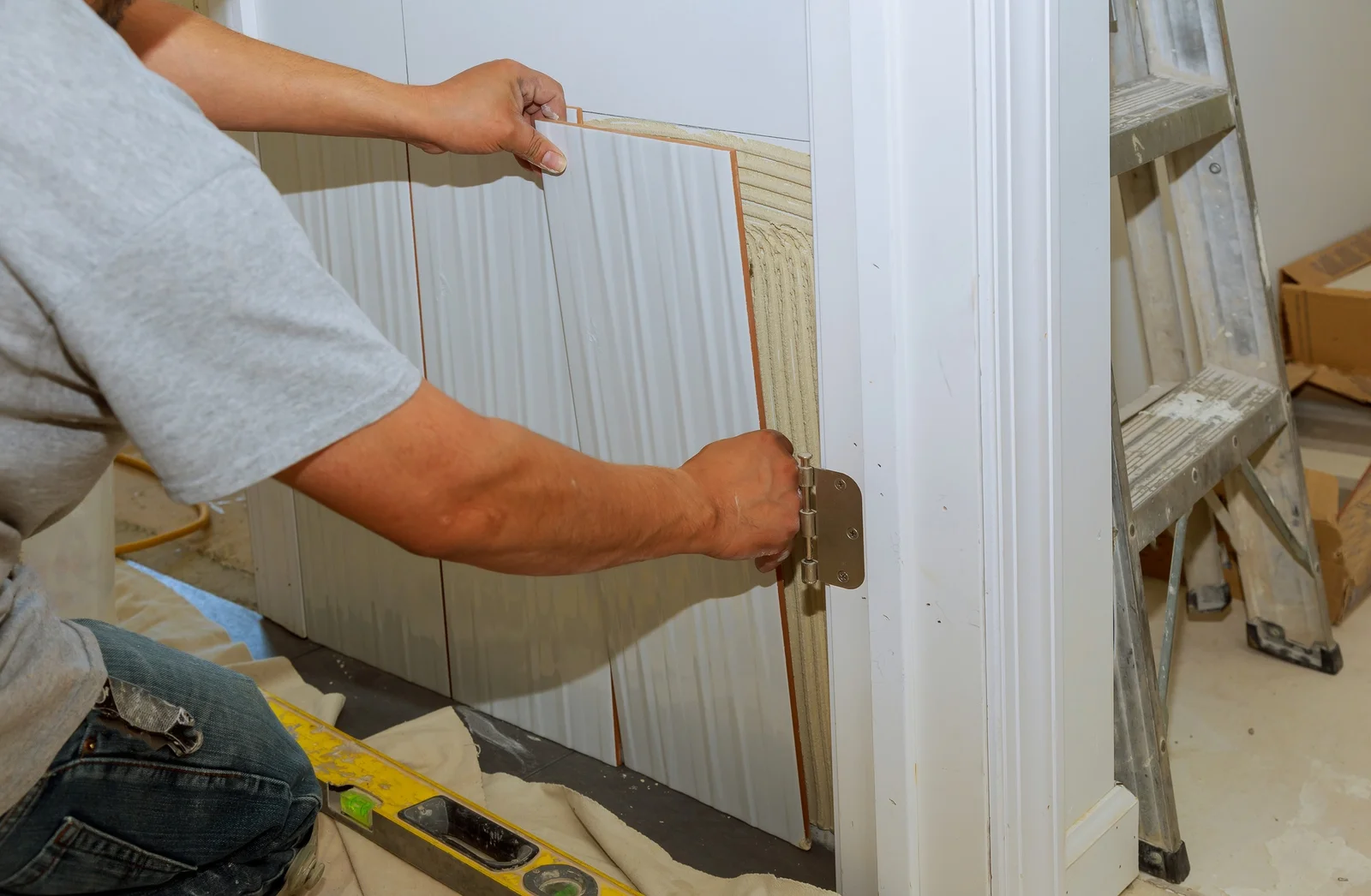
Introducción
Tile slippage during and after installation is a costly issue in construction, often leading to project delays, rework, and safety risks. Ensuring strong adhesion, particularly on vertical surfaces, is critical to meeting industry standards. HPMC (Hydroxypropyl Methylcellulose) offers an effective solution by enhancing cohesion, adhesive structuration, and water retention, ensuring tile adhesives meet the EN 1308 standard for slip resistance with performance below 0.5N/mm².
HPMC delivers anti-slip performance below 0.5N/mm² in tile adhesive by enhancing cohesion between the tile and adhesive, structuring the adhesive matrix for better grip, and retaining water for optimal curing. Its unique properties align with EN 1308 standards, ensuring tiles stay securely in place on vertical surfaces, reducing slippage, and enhancing construction safety.
Let’s explore why tile slippage matters, the forces at play, and how HPMC ensures superior anti-slip performance in tile adhesives.
The Cost of Tile Slippage and EN Standards
Tile slippage in construction can lead to significant financial losses due to rework, damaged materials, and extended project timelines. In environments like high-rise buildings, hospitals, or commercial spaces, improperly adhered tiles pose safety risks to occupants and workers. To mitigate these risks, the European Standard EN 1308 outlines the method for determining the slip resistance of tile adhesives on vertical surfaces.
According to EN 1308, the maximum allowable slip is 0.5mm for C and D type adhesives, ensuring that tiles remain in place during and after installation. Meeting this standard is essential for tile adhesive manufacturers aiming to deliver reliable, high-performance products.
- Industry pain point: 23% of tile failures due to slippage during installation (ETAG 004 data)
- EN 1308 Standard:
- Critical requirement: Anti-slip resistance ≤0.5N/mm²
- Test method: Vertical slip measurement under 0.3N/mm² shear stress
- HPMC value proposition: “87% of tested formulations achieve ≤0.4N/mm² with optimized HPMC”
Understanding the Physics of Tile Slippage
Tile slippage occurs due to the downward force of gravity acting on a tile adhered to a vertical surface. Key factors influencing slippage include:
- Gravity: Pulls the tile downward.
- Adhesive Viscosity: Determines the adhesive’s resistance to flow under load.
- Curing Time: The period during which the adhesive hardens and forms a strong bond.
The EN 1308 test protocol simulates real-world conditions by applying a standardized load to a tile fixed to a vertical surface with adhesive. The slip distance is measured, and adhesives must exhibit minimal movement to meet the standard.
- Typical failure thresholds:
- Ceramic tiles: >0.5N/mm²
- Large-format porcelain: >0.3N/mm²
EN 1308 test protocol breakdown:
- 20x20cm tile specimen
- 30-minute curing before vertical mounting
- Measured displacement under 50N load
HPMC, or Hydroxypropyl Methylcellulose, is a crucial additive in modern tile adhesives. It improves water retention, reduces water loss, and enhances adhesive performance, making it ideal for tiles that absorb significant amounts of water. By maintaining adequate moisture during curing, HPMC ensures that adhesives achieve optimal bond strength and workability.
HPMC is widely used due to its:
- High water retention capability
- Improvement of adhesive viscosity and stability
- Enhanced open time and workability of adhesives
HPMC’s Anti-Slip Mechanism in Tile Adhesives
HPMC enhances the anti-slip properties of tile adhesives through several mechanisms:
Cohesion Enhancement
- HPMC increases the internal bonding strength of the adhesive, ensuring that the adhesive layer remains intact and prevents tile movement under load.
- Viscosity optimization: 40,000–150,000 mPa·s HPMC grades
- Thixotropic index improvement: 1.8 → 3.2 (Brookfield RV test)
Adhesive Structuration
- By forming a stable and uniform adhesive matrix, HPMC provides a firm grip on tiles, reducing the risk of slippage during installation.
- 3D cellulose network formation (SEM imaging proof)
- Yield stress increase: 120Pa → 450Pa (Rheolab QC measurements)
Water Retention Advantage
- HPMC retains water within the adhesive mixture for a longer period, preventing premature drying and allowing the adhesive to cure evenly. This optimal curing ensures that the adhesive forms a strong, slip-resistant bond with the tile surface.
- Maintains 92% adhesive hydration during open time
- Reduces “dry drag” effect by 65%
Conclusion
HPMC offers unmatched anti-slip performance in tile adhesives, aligning with EN 1308 standards to ensure vertical tile safety. Its unique properties—cohesion enhancement, adhesive structuration, and superior water retention—make it an essential component for high-performance tile adhesives.
Ready to elevate your tile adhesive’s anti-slip performance? Póngase en contacto con nosotros to Explore the benefits of HPMC and enhance your product’s reliability today.